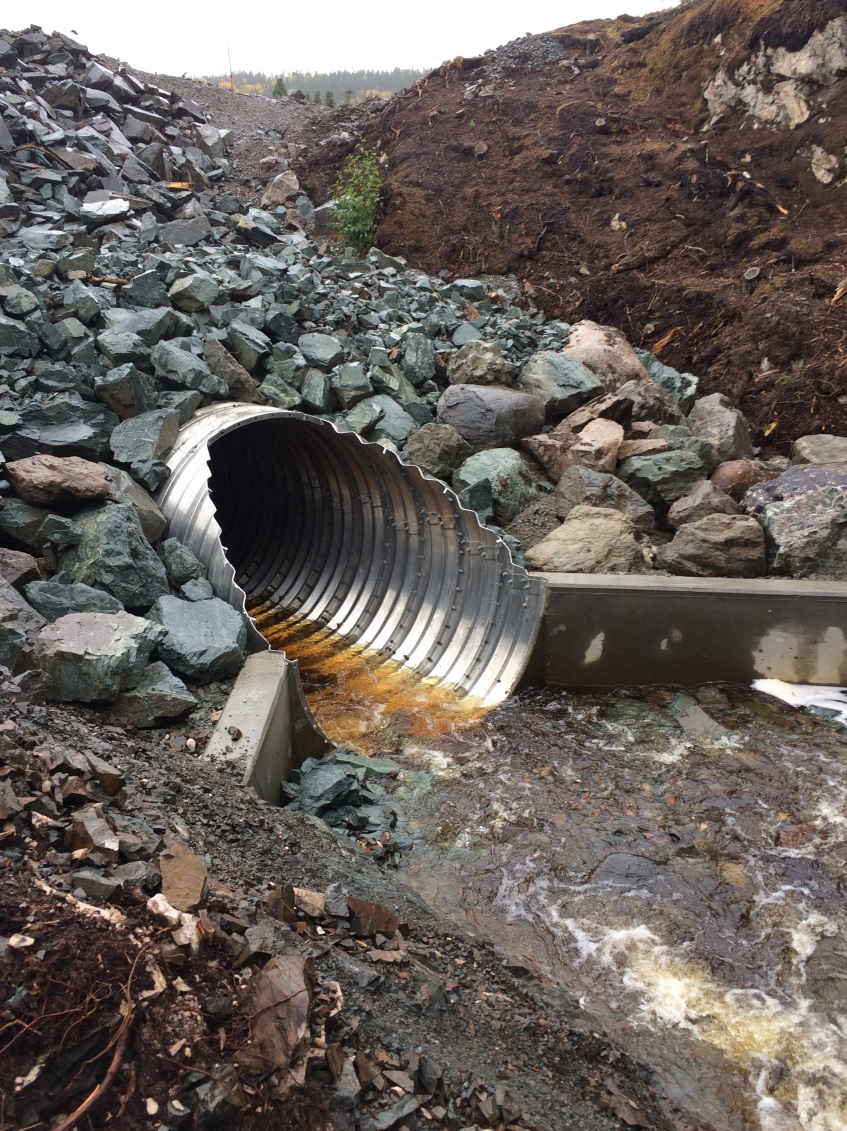
Terra Nova Tunnel Liner Plate Extension
Owner: Parks Canada
Engineer: Crandell Engineering
Contractor: J-1 Contracting
Location: Terra Nova National Park NL
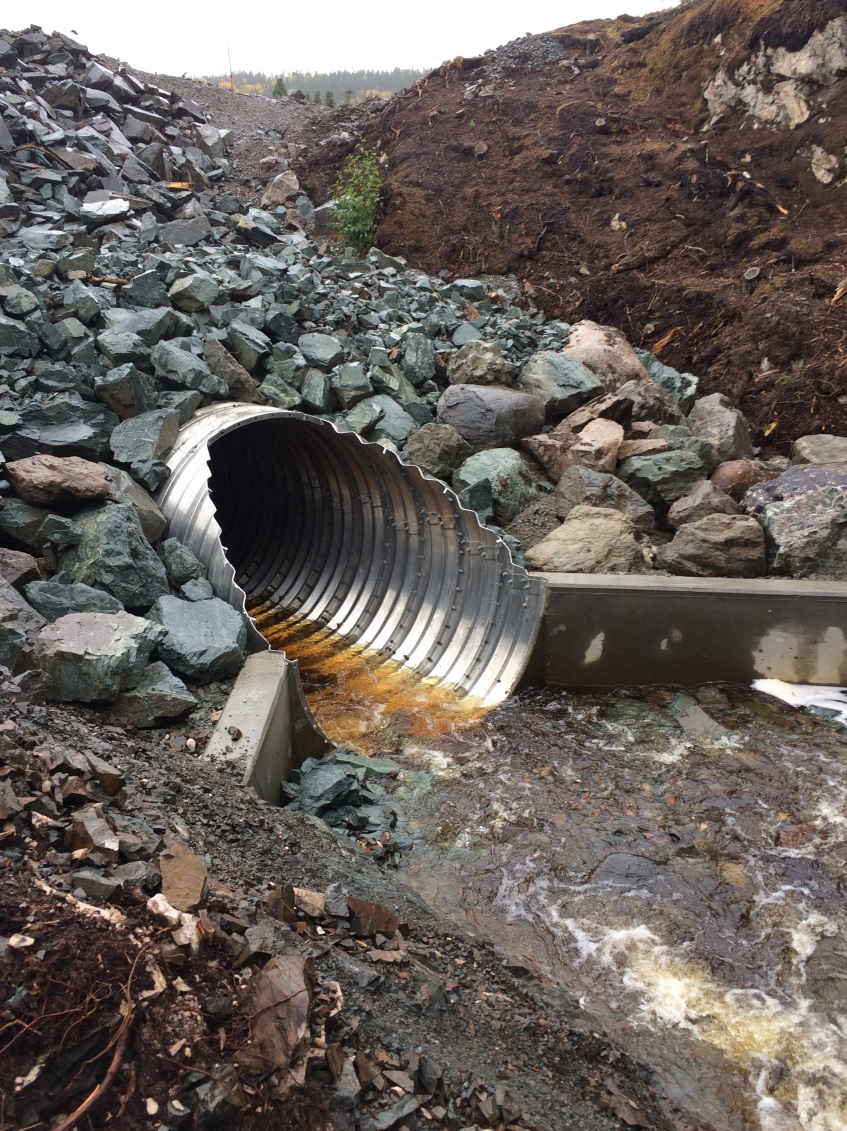
Product Utilized:
Tunnel Liner Plate
The Challenge
The existing Tunnel Liner Plate structure was at the bottom of a steep embankment, making access to the job site challenging. There was no infrastructure in place to allow easy movement of heavy materials or equipment. Terra Nova National Park is an environmentally sensitive area and home to a wide variety of wildlife. Any construction work had to minimize its impact on the natural habitat. Water levels were quite high in the existing culvert, which would make working conditions difficult. There were also large rocks directly in the path of the tunnel extension. As one of the busiest national parks in Canada, any construction work needed to minimize disruption to park visitors.
The Solution
Armtec’s ISO certified manufacturing facility in Guelph supplied 14m of 2,250mm diameter Aluminum Tunnel Liner Plate sections. The Aluminum material provided extended corrosion protection to withstand the hard water conditions on-site. Thanks to Tunnel Liner Plate’s lightweight properties, there was no need to construct access infrastructure which would negatively impact the park’s environmentally sensitive area. Each section weighed between 9 to 14 kg, making it light enough to be hand-carried from the road to the job site. A 10 inch pump was used to dewater the stream and provide access to the installation site. The largest rock obstruction was removed by breaking it down using a jackhammer. Extension of the Tunnel Liner Plate structure proceeded quickly. A crew of four assembled 20 rings per day, with 28 rings assembled in total. Since this section was an extension and not a reline, grouting was not required. There were no delays to traffic throughout the duration of the project. Installation, backfill and headwalls were complete in four days allowing widening of the road above and construction of the new passing lane.