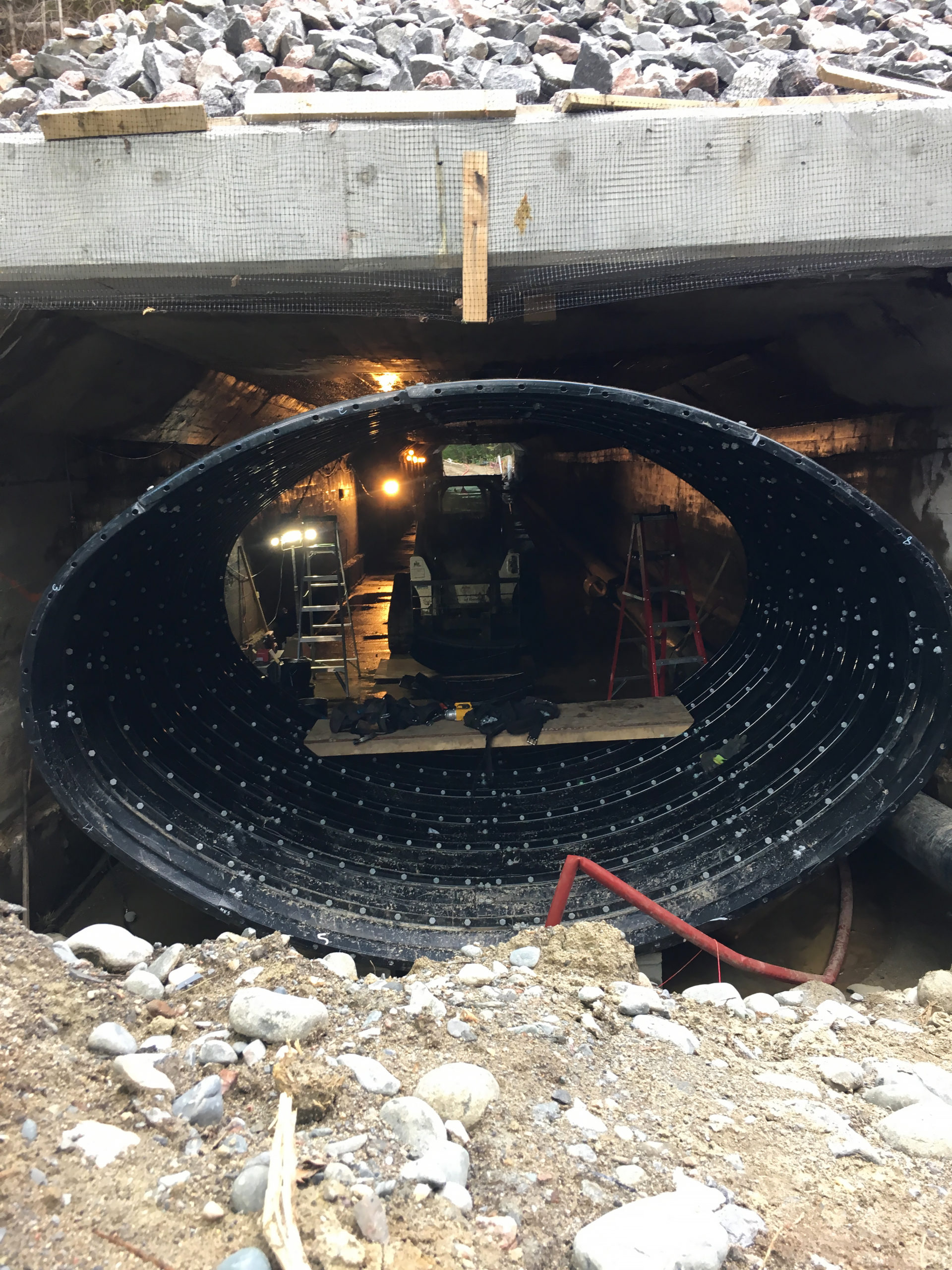
Shamrock Lake Tunnel Liner Plate
Owner: Ministry of Transportation Ontario
Engineer: Hatch
Contractor: Teranorth Construction
Location: Shamrock Lake ON
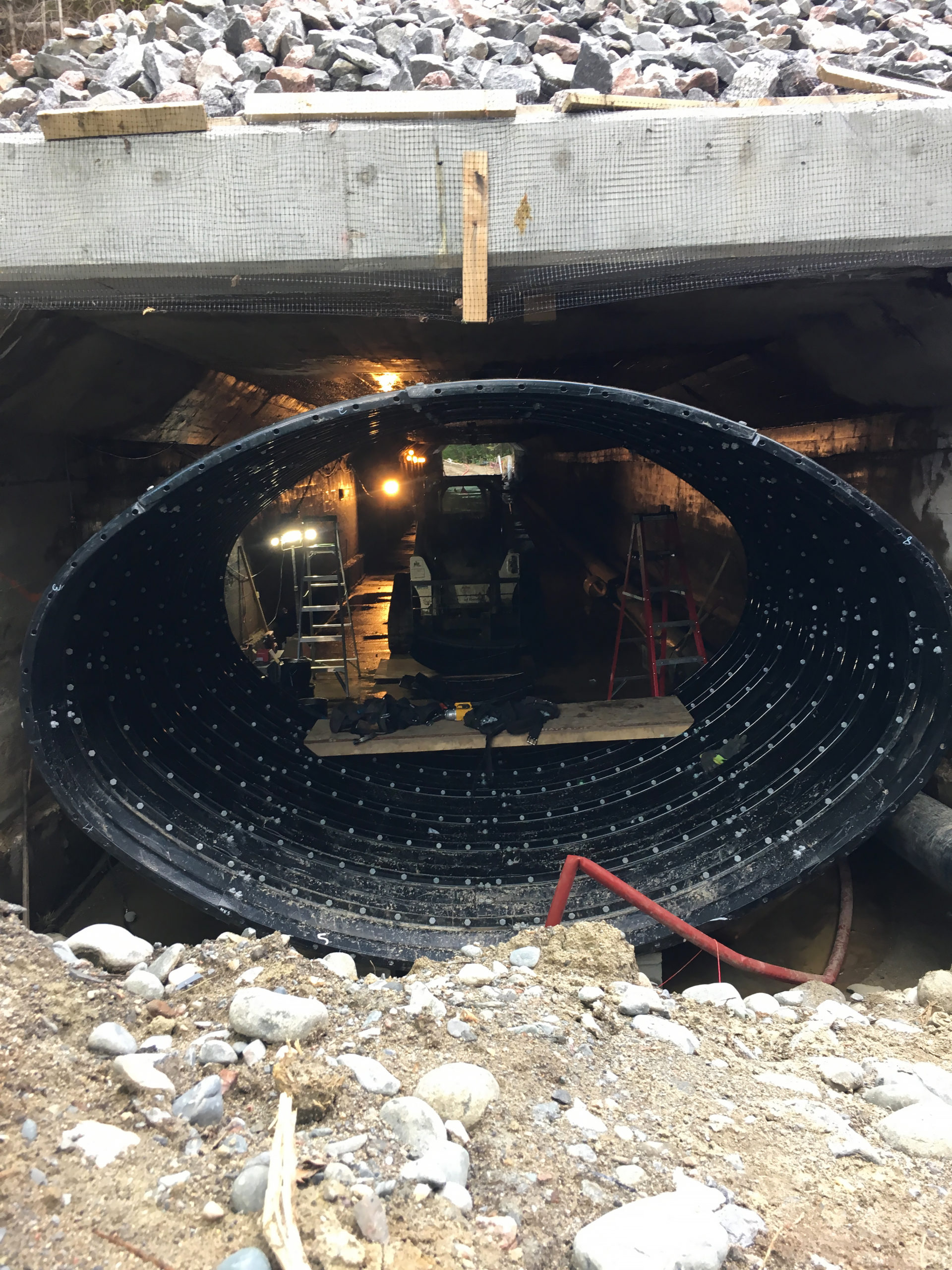
Product Utilized:
Tunnel Liner Plate
The Challenge
The location of the failing culvert proved to be one of the main challenges. Situated under 16.3m of cover within the Nipigon Palisades Conservation Reserve, the cost to excavate would be very high. The existing structure was long, measuring approximately 76m in length with a modest skew to the road, which presented an additional challenge if considering products that require a slip-lining installation. Access to the job site was also restricted given the steep slope of the incline and limited right-of-ways excluded from the conservation area, which in turn meant a usable construction lay-down area on the upstream side was not possible. Furthermore, handling and stockpiling the volume of excavated material was not feasible. Risks of undermining the existing footing with excavations at or below the elevation of the footings needed to be considered, as well as excavating in front of the footings, which may lead to loss of bearing capacity. Environmental regulations also required preservation of the local fish habitat.
The Solution
After considering several alternatives including replacement, TMB and pipe ramming, it was quickly concluded that rehabilitation of the existing concrete box culvert was the most viable option. Armtec proposed a horizontal ellipse Tunnel Liner Plate with a polymer coating to meet the 75 year DSL set out by the MTO. The structure was sized in order to ensure hydraulic requirements were met, despite the reduction in cross sectional area. The shape of the horizontal ellipse provided a higher conveyance than an equivalent round. Due to the length of the structure, slip-lining was ruled out as it would have introduced additional complexities to the project. This narrowed down the reline selection to products that could be constructed from inside the host structure. Armtec’s 2-flange Liner plate was chosen allowing installation to proceed completely within the existing culvert. The corrugation profile of the plate and its high steel strength provided adequate section properties to support the huge overburden loads without the need for costly excavation. As a modular structure with plates measuring only 500mm wide, Tunnel Liner Plate is ideal for locations with limited access. With the existing structure situated under 16.3m of cover and down a steep slope, the contractor built an access road angled across the incline. A bobcat drove plate segments directly into the culvert. Thanks to their light weight, plates were easily set into position by hand for installation, without the need for heavy construction equipment. The first stage of the installation involved cleaning out the old box culvert and pouring a new concrete floor. The existing structure was eroded and full of washed up rocks. With that complete, assembly of the Tunnel Liner Plate progressed completely from within the culvert. Shoring and blocking were used as the final stage before grouting. Since the invert of the existing concrete structure was heavily deteriorated, Armtec designed an invert beam to be welded at the bottom of the new liner, for the structure to be blocked against and to support the shoring jack force that fed through the socket at the obvert. Once grouting was complete and the shoring jacks removed, substrate retention sill plates were installed along the length of the culvert to reduce flow velocities and provide rest areas for fish travelling upstream. Tunnel Liner Plate allowed the safe and economical rehabilitation of this failing concrete culvert. Installation was completed in the summer of 2019 with minimal disruption to road users, most of whom were unaware of the busy job site below.